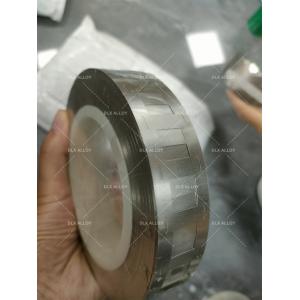
Add to Cart
Solderability Weldability Pure Nickel Strip For Precision Electronic Components
Elevate your engineering projects with our premium pure nickel strip, engineered for excellence and reliability. Whether used in aerospace, medical devices, or telecommunications, this strip meets the highest standards for performance and durability. Its low electrical resistance and high thermal conductivity ensure efficient energy transfer and heat dissipation, while its uniform composition and fine grain structure guarantee consistent results in every application. Trust our pure nickel strip to deliver the quality and performance you need for your most demanding projects.
Production Process
1. Raw Material Selection: The process begins with the selection of high-purity nickel. The nickel used is often in the form of nickel pellets or powders to ensure the final product's purity.
2. Melting and Casting: The selected nickel is melted in a controlled environment to prevent contamination. After melting, the nickel is cast into slabs or bars, depending on the desired end product's thickness and width.
3. Hot Rolling: The cast nickel slabs or bars undergo hot rolling, where they are heated to a specific temperature and passed through rollers. This process reduces the thickness of the nickel and increases its length.
4. Cold Rolling: After hot rolling, the nickel strip is further thinned through cold rolling. This process occurs at or near room temperature, enhancing the strip's strength and finish.
5. Annealing: The nickel strip is then annealed, a heat treatment process that relieves internal stresses, softens the material, and improves its ductility. Annealing is crucial for achieving the desired mechanical properties.
6. Slitting and Cutting: The annealed nickel strip is slit or cut into specific widths and lengths according to application requirements. Precision machinery ensures uniform and accurate dimensions.
7. Surface Treatment: The surface of the nickel strip may be treated through various processes, such as cleaning, polishing, or coating, to enhance its properties or appearance.
8. Quality Inspection: Finally, the nickel strips undergo thorough quality inspections. This includes testing for purity, thickness, width, and mechanical properties to ensure they meet industry standards and application needs.
Grade | Chemical Composition(%) | ||||||||
Ni+Co | Cu | Si | Mn | C | Mg | S | P | Fe | |
N4/201 | 99.9 | ≤0.015 | ≤0.03 | ≤0.002 | ≤0.01 | ≤0.01 | ≤0.001 | ≤0.001 | ≤0.04 |
N6/200 | 99.5 | 0.1 | 0.1 | 0.05 | 0.1 | 0.1 | 0.005 | 0.002 | 0.1 |
Applications
1. Battery Connections: Pure nickel strips are extensively used in battery manufacturing, especially for connecting cells in battery packs. Their excellent conductivity and corrosion resistance make them ideal for high-performance batteries, including those in electric vehicles (EVs) and portable electronics.
2. Electrical Equipment: In the electrical industry, nickel strips serve as key components in various equipment, providing reliable connections and enhancing conductivity.
3. Electronic Devices: Pure nickel strips are used in electronic devices for connectors, grounding straps, and shielding applications. Their properties ensure durability and efficient operation.
4. Corrosion-Resistant Coatings: Nickel strips are applied as protective coatings on other metals to prevent corrosion, especially in harsh environments.
5. Heating Elements: Due to their high-temperature resistance, nickel strips are used in heating elements for appliances like toasters, ovens, and industrial furnaces.
6. Chemical Processing: The chemical industry utilizes nickel strips in equipment that requires high corrosion resistance to withstand aggressive chemicals.
7. Aerospace and Defense: In aerospace and defense, nickel strips are used in components that require high strength, durability, and resistance to extreme conditions.